ESG Fume Incineration
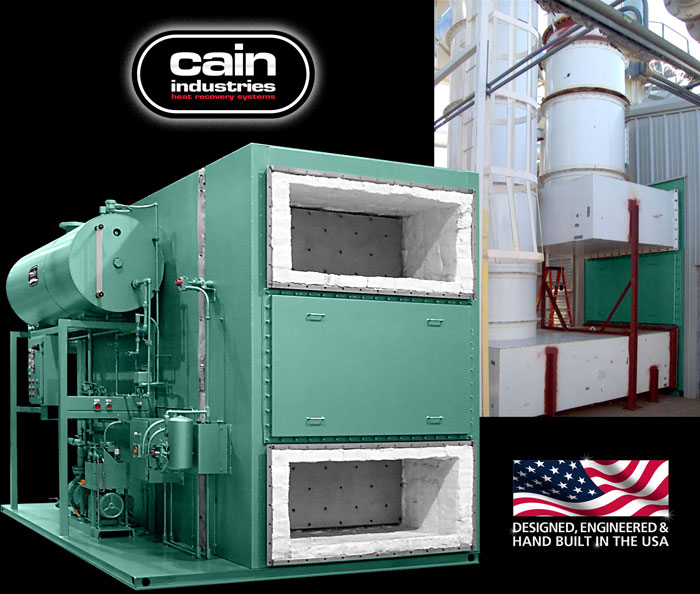
Exhaust Steam Generator
The ESG (Exhaust Steam Generator) is an unfired fully automatic, skid mounted packaged steam generator combining a finned tubing heat transfer section, steam flash circulating drum assembly, and full exhaust bypass. Where low or high pressure steam output demand is a necessity, the ESG in terms of recovered BTU/hr and its use, is a more valuable alternate selection to liquid or air preheat exchangers. The design allows for flexibility in heat transfer (explosion proof) output, lightweight design and compactness for lower installation costs, and will offer the greatest thermal efficiency.
The ESG accommodates outputs from 20 to 500 boiler horsepower with operating steam pressures ranging from 3 to 450 PSIG. Engineering design consideration has been given to complexities and flexibility requirements of steam generation, and retrofitting the engine and fume incineration market. Important areas of concern are: controlling and bypassing waste heat, optimum performance selection, operating pressures, size, weight, and ease of installation. The ESG addresses concerns with standard design features important to the designer, packager, and customer which are not usually found in conventional waste heat firetube boilers.
The extremely lightweight, compact design includes three basic sections: the fin tube heating surface, steam flash drum assembly, and a modulating full-port exhaust bypass pre-piped and wired for ease of installation and minimal customer connections. The integral circulating pump continually circulates water to the heat transfer section recovering BTU from the exhaust, and back to the steam drum assembly where the water is flashed to steam. Coupled with the ESG's capacity to produce and control supplemental or primary steam output, it's unique design allows for full output in approximately 10 to 15 minutes and is fully automatic under fluctuating loads. The ESG is a packaged forced circulation watertube design, manufactured and tested in accordance with the requirements of Section VIII, Division I of the ASME Boiler and Pressure Vessel Code, and stamped to the appropriate section.
Combustion Sources
Incinerators, thermal oxidizers and catalytic converters
Exhaust Application
Capacity: 1,000 to 50,000 SCFM
Entering Gas Temps: 600°F to 1,600°F
Heat Sink Types: supplemental steam demand and/or primary steam source for steam heating or process steam
- Steam Flash Drum Assembly
- Inspection and Tube Removal Door
- Fully Modulating Internal Exhaust Bypass
- Circulating Pump Assembly
- Pneumatic Modulating Damper Actuator
- Control Panel Assembly
- Boiler Blowdown Systems
- Boiler Feedwater Economizer
- Boiler Feed Condensate Return Systems
- 1/3 to 1/2 the Weight, Size, and Floor Space
- 99% Dry Steam
- 100% Turndown Capacity
- 5 to 10 Minute Startup to Full Output
- Integrated Full Exhaust Modulating Bypass
- "Explosion Proof" Heat Transfer Exchanger
- Low Friction Loss for Minimum Static Exhaust Back Pressure
- High Circulating Flow Minimizes Scale Buildup
- No Thermal Expansion Problems: Accepting Cold Water Boiler Feedwater
- Lowest "Pinch Point" (final leaving exhaust temperature minus operating steam temperature) Offering Greater Thermal Efficiency